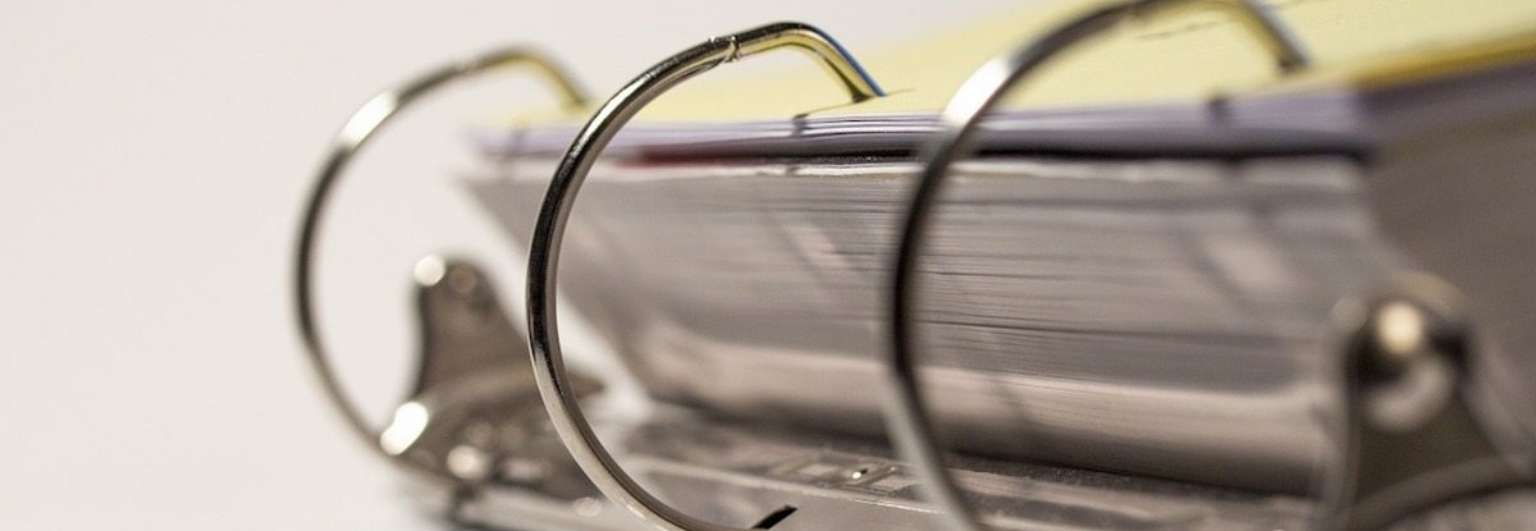
28 Nov Creating an Effective Workplace Safety Manual
Many companies do not have a workplace safety manual, or if they do have one, it is often outdated or too long and complicated. This is unfortunate because a well thought out safety manual can help your business in many ways.
First, it can help prevent workplace injuries and illnesses and reduce claims and insurance costs. Second, a well-crafted manual improves legal and regulatory compliance. Third, it engages workers and improves productivity, which benefits business operations and your bottom line.
Here’s what you should consider when creating a safety manual for your company.
Make It Workplace Specific
Many companies offer safety manual templates, and they’re a great place to start. However, they don’t offer the detail you’ll need to make it really work for your business.
Create your manual specifically for your work environment, but use lay terms. Only include what is absolutely necessary – no fluff or filler. You want every person to understand what you’ve written so they can follow your safety message easily and routinely.
What To Include
Here are some general topics most companies include in their workplace safety manual.
General Health & Safety Policy – describes your company’s overall safety goal, major stakeholders such as employees, management, and regulatory bodies, and a brief description of how you see everyone working together towards safety.
Workplace Hazard Assessment – The Occupational Safety and Health Administration (OSHA) requires employers to conduct inspections of all workplaces or tasks to determine if hazards are present that would require the use of Personal Protective Equipment (PPE). They provide step-by-step procedures on their website. You can use this checklist to identify risks and equipment needs.
Company Rules – These are general rules that apply to all employees. Examples include wearing appropriate PPE when and where required, workers following safe work practices and safe job procedures in the workplace, maintaining good housekeeping, zero tolerance for theft or vandalism, etc. SafetyInfo.com provides a free customizable document to assist you with the process.
Safe Work Practices – Safe work practices are documents that outline how people should perform a task to minimize risk. These often include things such as using ladders, scaffolding, vehicles, forklifts, or other equipment. Here is an example from Virginia Tech on ladders.
Safe Job Procedures – are a series of specific steps to guide workers through a specific task from start to finish in order. Here is an example from OSHA on portable step-ladders.
Preventive Maintenance – companies in specific industries or ones that use certain equipment perform mandatory inspections, however voluntary inspections improve workplace safety for all businesses. Here is an example regarding reducing risk through preventive silica maintenance.
Training and Communications – describes how your company trains and communicates with workers. Here’s an example from Stanford Environmental Health & Safety.
Inspections, Investigations and Reporting – describes when, what, and how frequently you perform inspections, how your company investigates incidents, and the reporting procedure.
Emergency Preparedness – OSHA offers in-depth information describing what you need to do to protect employees in an emergency.
Records & Statistics – OSHA has very specific recordkeeping requirements. You can find information on who needs to keep records and which forms you need to submit on their website.
Additional Considerations
Companies may also want to include industry specific information, such as back injury prevention if your employees do heavy lifting. Businesses that work with chemicals often include their environmental policies, but all companies benefit from transparency.
Many businesses include information on their substance abuse prevention or health and safety committee, too. Employees are more likely to seek assistance when they know that your company has clear plans and designated representatives to handle their issues.
You may also want to include your claims management system to avoid confusion and to lay out the process clearly.
OSHA’s Small Business Handbook is an excellent resource to help you think of issues that may apply to your business and what to include in your safety manual. It also includes checklists and worksheets to help you draft policy statements and safe practices. You may also want to use their training manual template and develop it specifically for your business.
If your company does not have a workplace safety manual, start now. It is a top priority and at the center of your company’s safety system. If your safety manual is gathering dust on a shelf somewhere, dust it off and review it for clarity and accuracy.
Remember, it is important that you implement and monitor policies and procedures in all areas of your operation. Monitoring shows what works and what needs further attention.
The team at Gilbert’s Risk Solutions is focused on risk management. We can help you reduce your insurance costs, create a safer workplace, and streamline your processes.
We’re local and reliable and easy to talk to, so contact us to discuss your insurance needs. We’ve helped companies for over 160 years, and we’re here for your business, too. Let us show you how we can help.
No Comments