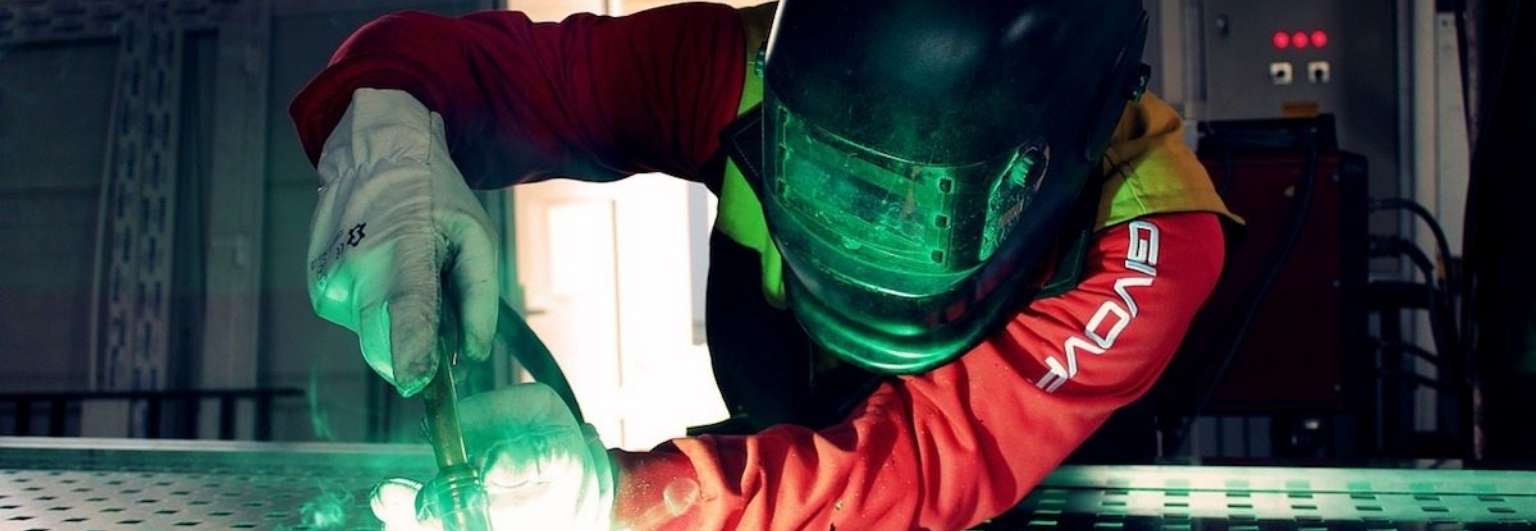
29 Jun Reduce Your Insurance Rates by Increasing Workplace Safety
The manufacturing industry comes with many risks, and protecting your employees against injuries is a basic cost of doing business. However, many manufacturing businesses don’t realize that relying on insurance alone for protection is neither wise, nor cost-effective.
Workplace Risk Affects More Than Premiums
Injuries and illness in the workplace cost much more than increased insurance premiums. When someone must take time off from work, it lowers productivity and reduces profits. If a skilled worker cannot return to work, you’ll need to recruit and train a new employee, which costs substantial time and money.
An unsafe workplace can also negatively impact the quality of your product and your company morale. Word travels fast, and people do not want to work for a company that does not protect its employees.
Current employees will not be as productive, attentive, or loyal and turnover rates can increase. Attracting new employees may become a major issue, and you could need to pay higher than normal wages to get the people you need.
When a manufacturing company or their employees do not follow safety protocols, it can also lead to equipment failure or damage. Unnecessary capital costs can cripple some companies, or at the very least severely impact their bottom line.
Companies that ignore safety are only harming themselves. According to The American Society of Safety Engineers, workplace injuries cost one-quarter of each dollar of pre-tax corporate profits each year, and indirect costs may cost 20 times more.
Conversely, a safe workplace positively benefits your brand, your employees, and your profits.
Safety Is Everyone’s Responsibility
Safety in the workplace goes beyond policies. Communication and employee participation are an integral part of any successful work safety program. Management should encourage employees to identify unsafe situations, and employees should learn and use proper safety protocols.
Regular Breaks
When you’re on a production deadline, productivity is paramount. However, manufacturing involves many potentially hazardous machines, and if an employee hurts themselves or damages a machine, it will cost far more than a short break. Ensure employees take the breaks they need to rest and restore concentration.
Proper Training
Employees need to know how to use tools and machinery properly. Stress the importance of using the right tool for the job and mentor a new employee under a seasoned worker so they understand the risks of specific machines. Show them which safety equipment they need to use for each task.
Let your employees know they have a responsibility to report unsafe conditions to their supervisor so it can be corrected before someone gets hurt. Clearly define the risks and consequences of employee drug or alcohol abuse as well as failure to use safety equipment.
Clear Workspace
One of the simplest and most effective ways to decrease claims is by keeping the workspace clean. Employees should clean up spills immediately and remove loose objects that could fall or cause a person to trip.
Clear away obstructions from emergency exits and shutoffs, too. Clutter can make it impossible for employees to use tools properly or pick up heavy objects without straining their back.
Monitor Employee Stress
Manufacturing can include long hours and a heavy workload. Supervisors should monitor employees for signs of stress and address problems as they arise. If you’re on a deadline, consider assigning complex work at the start of a shift. Don’t ignore conflict between employees or managers, either. It impacts concentration and increases risk.
Reducing Insurance Premiums
Insurance carriers measure the costs of workers’ compensation benefit claims, civil liability damages, and litigation expenses when they look at the manufacturing industry. Claims may include employees, contractors, or even visitors on your worksite.
Insurers also rely on factors such as the number of employees on the payroll, the work performed, and your experience mod to establish your base premium rate. However, you have an opportunity to improve safety in your business to earn a discount if your claims costs are lower than similar competitors facing similar risks.
When fewer employees hurt themselves or become ill, the insurance company pays out fewer claims. According to the Occupational Health and Safety Administration, successful health and safety programs reduce injury and illness costs by between 20 and 40%. Consequently, employers can reduce out-of-pocket expenses and reduce insurance premiums when they tend to workplace safety.
Gilbert’s Risk Solutions’ long track record and commitment to excellence can help you reduce your insurance costs. We’re local, reliable and easy to talk to, so contact us to discuss your insurance needs. We’ve helped companies for over 160 years, and we’re here for your manufacturing business, too.
No Comments