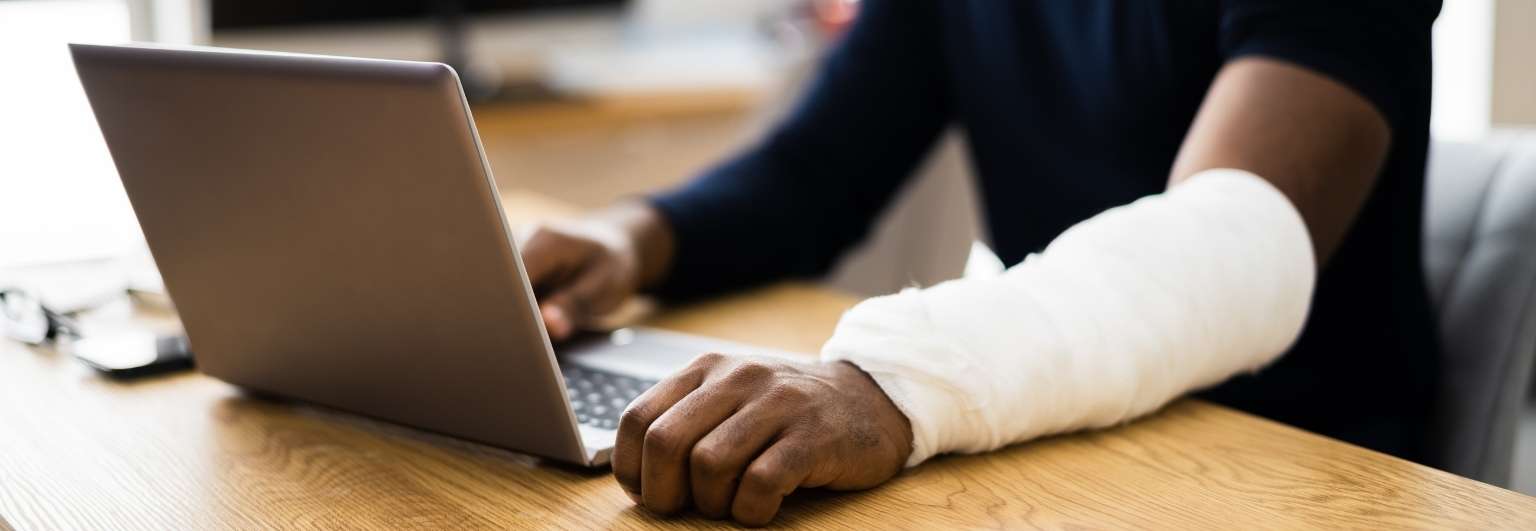
27 Jul How to Avoid 6 Common Workers’ Compensation Claims
Improving employee safety reduces Workers’ Compensation claims, improves productivity and morale, and lowers insurance premiums.
According to the 2016 Pennsylvania Workers’ Compensation & Workplace Safety Annual Report, 159,170 injuries and 77 deaths occurred in the workplace. The most claims occurred in Educational & Health (hospitals, nursing homes, schools), Trade, Transportation & Utilities (retailers, warehouses, transport companies, etc.), and Manufacturing, but no industry is immune.
Total compensation paid through commercial insurance carriers, State Workers’ Insurance Fund, individual self-insurers, and group self-insurance funds was almost $3 billion. Even minor injuries impact operations and productivity, so it’s always in a company’s best interest to create a safer workplace.
These are 6 of the most common forms of injuries to workers in the state, and how you can avoid them.
Sprains or Strains (37.8%)
Sprains and strains, due to improper lifting, pulling, and pushing, top the list of workplace injuries and over a third of these injuries occur in the torso. Companies can reduce their liability significantly by identifying risks and implementing controls.
Jobs requiring excessive force, repetition, or awkward body movements are common causes of sprains and strains. Businesses can educate employees in prevention principles such as proper lifting and control hourly or daily production targets to reduce repetitive strain.
Contusions, Crushings, & Bruises (18.2%)
Employee injuries caused by falling or flying objects is the next leading cause of injury. Most contusions, crushes, and bruises (31.8 percent) occur in the lower extremities.
According to OSHA, problems include machinery with unguarded moving parts, using unstable machinery, using machinery improperly, employee inattentiveness and/or failing to use proper safety equipment, and a cluttered, unsafe work area.
Employers have a responsibility to ensure worker safety. They must take measures to minimize clutter, train employees properly, and provide appropriate safety equipment. They must also designate a competent person to oversee safety in the workplace.
Cuts, Lacerations, & Punctures (16.7%)
Most cuts, lacerations, and punctures occur in the upper extremities (73.6 percent). Risk factors include improper training, employee inattentiveness or rushing to complete work, failure to wear proper protection or use safety guards, using an incorrect or ineffective tool, and workplace clutter.
According to PA Training for Health & Safety, the number one way to prevent cuts and lacerations is to ensure employees wear appropriate personal protective equipment (PPE) for the job being done. Employers must provide proper training and ensure safety equipment and supervision for compliance.
Fractures (3.9%)
According to American Academy of Orthopaedic Surgeons, most fractures occur from trauma. Slips and falls, vehicle accidents, falling objects, equipment malfunction, and a lack or disregard for safety standards can all cause fractures.
Employers must ensure scaffolding and ladders are properly maintained and work areas are well-lit. They must also train employees in the proper use of appropriate safety gear, ensure vehicles and machines are in good working order, and provide specific training for equipment such as forklifts.
The work area must be free of debris and wet or slippery floors must be cleaned quickly and marked with signs.
Heat and Chemical Burns (1.9%)
Three main types of burns occur in the workplace; thermal (heat), chemical, and electrical. Employers must review the risk to employees and implement controls to reduce the likelihood of injury.
Employee training is critical when employees work in high heat environments, with dangerous chemicals, or on electrical components. Workers must thoroughly understand the risks, required safety equipment, and proper procedures to avoid accidents – such as using Safety Data Sheets (SDS) for chemicals.
Employers can further reduce their risk by limiting employee exposure to heat and chemicals, storing combustible and flammable materials properly, and by keeping the workplace clear of debris.
Occupational Illnesses (1.8%)
The Pennsylvania Occupational Disease Act defines the “liability of an employer to pay damages for occupational disease contracted by an employee arising out of and in the course of employment.” In a landmark 2014 case, the courts also found employers responsible for latent occupational diseases.
Obviously, exposing an employee to any of the controlled substance in the act can have grave long-term financial, reputational, and workplace repercussions.
Companies that work with toxic chemicals or in dangerous environments must follow strict health and governmental protocols to ensure employee safety. Anything less could find them liable for ongoing medical costs and compensation.
Many companies sell insurance products, but few take the time to analyze your needs. Gilbert’s Risk Solutions’ long track record and commitment to excellence minimizes risk and cost. We’re local and reliable and easy to talk to, so contact us to discuss your insurance needs. We can help your company reduce your risk and your Workers’ Compensation claims.
No Comments